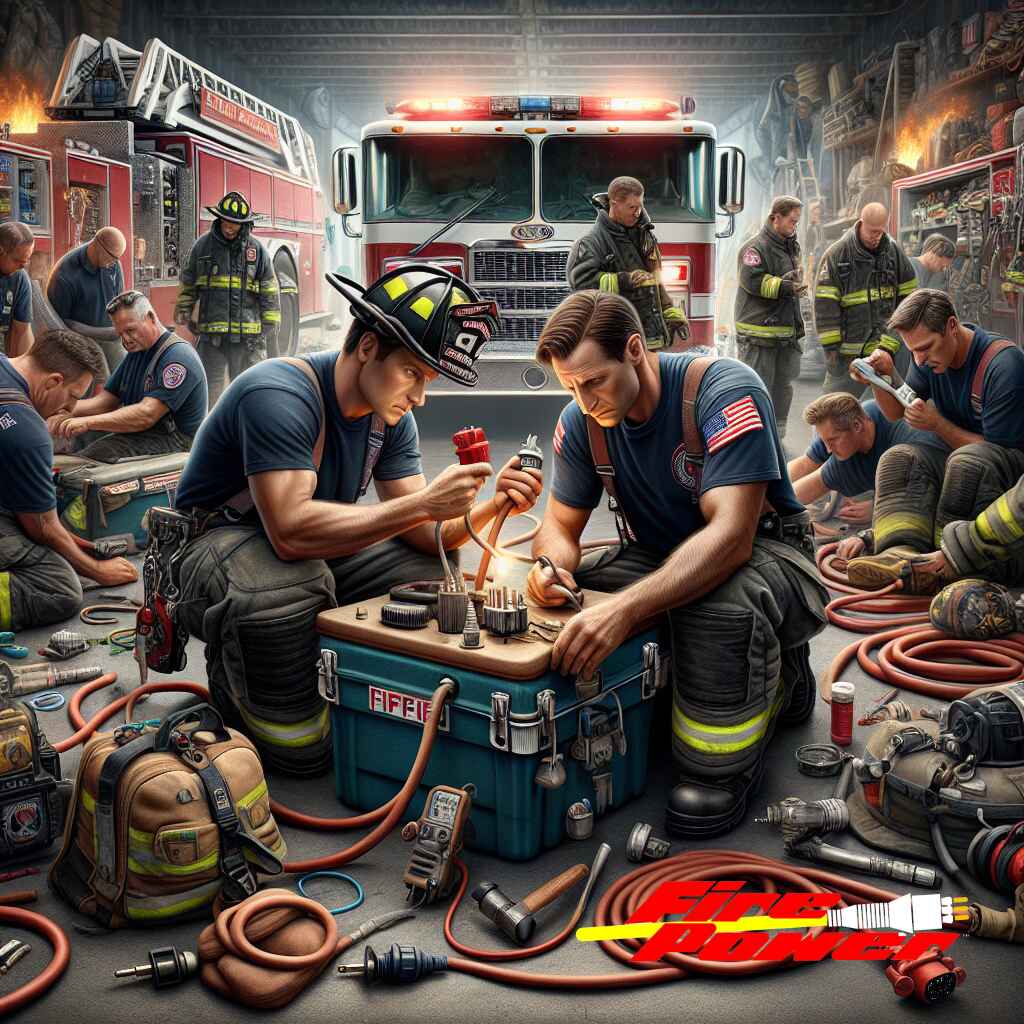
Best Practices for Maintaining Fire Power Products
December 23, 2024
Firing Up Your Knowledge of Fire Power Product Maintenance
The importance of maintaining Duraline fire products
Maintaining Duraline fire products is crucial for ensuring the safety and efficiency of first responders and EMS personnel. These products, designed to withstand the rigors of firefighting and rescue operations, demand regular maintenance to preserve their functionality and reliability. The importance of this upkeep cannot be overstated, as it directly impacts the life-saving capabilities of fire departments and emergency services. Regular maintenance ensures that all components, from electrical connectors for fire fighting to high-pressure hoses, perform optimally under pressure, reducing the risk of malfunction or failure during critical moments.
Adhering to a strict maintenance schedule helps in identifying wear and tear before it leads to bigger issues. Ensuring that all equipment is in top condition means that when they are called into action, they function as expected, providing superior performance that first responders rely on. It’s also about longevity, maintenance extends the service life of these products, offering better value over time and ensuring that investment in quality firefighting equipment pays off in the long run.
Understanding the unique needs of first responders’ equipment upkeep
First responders’ equipment is subjected to some of the most demanding conditions imaginable. From high temperatures and exposure to flames to physical impacts and water damage, this gear needs to be as resilient as the personnel who use it. Understanding these unique needs is the first step in effective maintenance. It entails a comprehensive approach that goes beyond simple checks and cleaning.
Special consideration should be given to the durability and operational readiness of the equipment. This includes thorough inspections for signs of damage, testing under simulated conditions to ensure performance is not compromised, and regular updates or replacements of parts that are prone to wear and tear. For instance, performing routine checks for fire gear readiness ensures that when a firefighter rushes into a blaze, their equipment will function without a hitch, safeguarding not only their life but also the lives they are working to save.
Setting the stage for EMS gear maintenance and durability
EMS gear, which includes a wide range of equipment from defibrillators and stretchers to personal protective equipment, requires a tailored maintenance approach to ensure durability and reliability. Setting the stage for effective EMS gear maintenance involves implementing a systematic and thorough inspection routine that accounts for the unique challenges faced by medical first responders.
One of the key aspects of setting this stage is education and training. EMS personnel must be equipped with the knowledge to perform basic maintenance checks and recognize when professional servicing is needed. This proactive approach to maintenance can significantly impact the effectiveness of response efforts in emergencies. It’s not just about keeping the equipment in working order, it’s about ensuring that when an EMS professional reaches for any piece of gear, they can do so with confidence, knowing it will perform as needed in the critical moments where it matters most.
Routine Checks for Unbeatable Performance
Scheduling regular inspections for firepower parts
To uphold the unmatched endurance and performance of product maintenance, setting a regimented schedule for inspections is paramount. The longevity of firefighting parts hinges on the ability to detect and address potential issues early. Implementing a structured inspection routine helps in identifying wear, tear, or malfunctions that could compromise the operational efficiency of these tools. It’s advisable to conduct these inspections following the guidelines established by the manufacturer, leaning on their expertise to ensure each component is examined rigorously. This practice not only promotes the safety of first responders but also enhances the resilience of the equipment against the challenging environments it encounters.
Key aspects of fire trucks’ electrical maintenance
The electrical systems of fire trucks serve as the nerve center for operations, facilitating communications, lighting, and the operation of water pumps. Given the complexity and critical nature of these systems, fire trucks’ electrical maintenance demands thorough attention. A comprehensive approach to maintenance includes checking battery connections for corrosion, ensuring wiring is intact and free from damage, and verifying that all electrical systems are properly grounded. Regular functional tests of the electrical components can preempt failures during critical missions. Additionally, keeping abreast of the latest updates and recommendations from vehicle manufacturers can guide the maintenance protocol, ensuring that each fire truck remains responsive and reliable when it matters most.
Ensuring electrical connectors for fire fighting are fault-free
Electrical connectors play a pivotal role in the seamless operation of firefighting equipment, bridging various components for power and communication flow. Ensuring the reliability of firefighting equipment rests on the integrity of these connections. It is essential to regularly inspect connectors for signs of damage, such as cracks, corrosion, or loosening, that may hinder their functionality. Utilizing high-quality connectors, designed to withstand the harsh conditions of firefighting, further guarantees the sustainability of operations. Applying dielectric grease can prevent corrosion, and ensuring a firm connection mitigates the risk of power loss. By instituting a meticulous check for the health of electrical connectors, departments can significantly reduce the likelihood of equipment failure, underscoring the critical importance of these components in maintaining operational readiness.
Navigating Through Rough Conditions
Protective measures for firepower products in adverse environments
In the demanding world of fire fighting and emergency response, Fire Power products by Duraline are engineered to not only meet but exceed the expectations of durability under rough conditions. However, even the toughest equipment requires protective measures to ensure their longevity and dependability when facing adverse environments. Implementing protective practices is critical, from utilizing protective casings and covers to minimize exposure to heat and chemicals, to the strategic storage of equipment to shield it from the elements. Ensuring that Fire Power products are properly cleaned and inspected after exposure to harsh conditions can significantly reduce the risk of damage. These steps are essential for safeguarding the integrity of the equipment, ensuring that it remains ready and reliable for the next call to action.
Maintaining high-pressure resistance in firefighting equipment
High-pressure resistance is a hallmark of quality firefighting equipment, enabling it to perform under the most demanding conditions. To maintain this critical feature, regular checks of hoses, electrical connectors, and nozzles are indispensable. It is vital to search for any signs of wear and tear, such as cracks or leaks, that could compromise the equipment’s ability to operate under high pressure. Substituting worn parts promptly and adhering to manufacturers’ specifications for use and maintenance can help preserve the high-pressure capabilities of firefighting equipment. Adhering to these practices not only extends the service life of the equipment but also ensures the safety of the operatives relying on them in life-saving situations.
Handling wear and tear from frequent use and abuse
Duraline’s Fire Power products are subjected to frequent use and abuse in the line of duty. Wear and tear will inevitably occur, but with the right maintenance approach, the impact can be minimized, and the lifespan of the electrical equipment extended. Implementing a routine check for deployment readiness, including thorough inspections for physical damage and operational testing, is a cornerstone of effective wear and tear management. Any identified issues should be addressed promptly to prevent further degradation and faults. Furthermore, educating first responders on the proper use and handling of equipment can reduce unnecessary strain while under load and extend the operational life of these critical tools and connected accessories. Together, these strategies form a comprehensive approach to managing the wear and tear of firefighting equipment, ensuring they remain in peak condition for every call.
The Path to Longevity and Reliability
Preventing fire product malfunction with proactive care
The functionality of Fire Power products directly impacts the safety and efficiency of first responders. Proactive care is essential in preventing equipment malfunctions that could compromise emergency operations. Regularly scheduled maintenance, including the routine check for fire gear, allows for the early detection of potential issues that may lead to equipment failure.
Adopting a proactive approach involves keeping abreast with the latest service bulletins and updates from the manufacturer, ensuring that all equipment complies with the current standards and recommendations. Incorporating real-time monitoring technologies, where applicable, can also provide instant feedback on equipment status and alert responders to any required maintenance. By prioritizing preventative measures, departments can maintain a state of readiness and reliability of their equipment, mitigating risks before they escalate into critical failures.
Securing a long service life for fire gear through meticulous upkeep
Ensuring a long service life for fire gear aligns with the principles of sustainability and cost-efficiency. Through meticulous upkeep, including comprehensive inspections, cleaning, and repairs, departments can elevate the durability and functionality of their firepower products. A key aspect of extending the lifespan of firefighting equipment is understanding and adhering to the specific maintenance protocols outlined in the fire power products service guidelines.
By regularly conditioning protective fabrics and confirming the integrity of electrical connectors, departments can prevent premature wear and enhance the protective capabilities of their gear. Additionally, adopting a system of rotation for equipment usage can evenly distribute wear, further prolonging the service life of critical firefighting assets. Investment in advanced training for maintenance personnel ensures that they are equipped with the knowledge and skills to meticulously care for equipment, securing their long-term reliability and performance in the field.
The Art of Superior Equipment Care
Leveraging Superior Performance Upkeep for EMS Gear
EMS gear is indispensable in providing timely and effective medical services, making its maintenance a top priority. To ensure EMS gear retains its reliability and superior performance, adopting a meticulous upkeep regimen is essential. Regularly scheduled cleaning, inspections, and functional tests form the cornerstone of this regimen. Specifically, EMS gear maintenance includes examining medical devices for accuracy, sterilizing equipment to prevent contamination, and ensuring all mechanical parts operate smoothly. Adhering to manufacturer guidelines for care and promptly addressing any signs of wear or malfunction ensures EMS gear is always in peak condition, ready to save lives.
Moreover, training EMS personnel in the proper use and routine maintenance of their equipment can significantly enhance its longevity and performance. Live training with equipment, with hookups to EMS vehicles utilizing Duraline’s Fire Power connectors, teams can become more attuned to detecting early signs of equipment failure, allowing for swift corrective actions that prevent delays in emergency response. Ultimately, leveraging superior performance upkeep for EMS gear not only guarantees the readiness of medical first responders but also underpins the quality of care delivered to those in need.
The Critical Role of Electrical Connectors in Ensuring Fire-Fighting Efficiency
The seamless operation of firefighting equipment heavily relies on the integrity of its electrical systems, where electrical connectors play a pivotal role. These connectors facilitate the power and information flow essential for the operation of various firefighting tools and apparatus. Ensuring electrical connectors are fault-free is crucial for the uninterrupted functionality of firefighting gear, from radio communication devices to water pump controls.
Given their exposure to extreme conditions, including high temperatures and moisture, these connectors must be robustly designed and meticulously maintained. Routine inspections help identify potential issues such as corrosion or loose connections, which can significantly impede firefighting efforts if left unaddressed. The proactive replacement of worn or damaged connectors, coupled with the application of protective lubricants to resist corrosion, assures the reliability of firefighting equipment. This preventive approach not only enhances firefighting efficiency but also ensures first responders can perform their duties with confidence in their equipment.
Enhancing the Durability and Reliability of Fire-Fighting Gear
The harsh operational environments encountered by fire fighting gear necessitate an advanced level of care to maintain its durability and reliability. Adopting strategies that mitigate the adverse effects of such conditions is paramount in prolonging the service life of this critical equipment. Key to this endeavor is emphasizing the importance of cleaning and proper storage. After exposure to smoke, chemicals, and debris, thorough cleaning removes potentially corrosive substances, while correct storage shields the gear from environmental damage.
Another aspect of enhancing durability involves conducting regular stress testing under simulated conditions, which provides an accurate assessment of the gear’s resilience and operational readiness. This allows for the identification and rectification of potential weaknesses before they compromise performance in real-world scenarios. Additionally, staying abreast of technological advancements and integrating modern materials and designs can further augment the gear’s resistance to wear and tear.
Fostering a culture of continuous improvement and proactive maintenance within fire departments empowers first responders by equipping them with gear that performs reliably under the most extreme conditions. By diligently caring for fire fighting equipment, departments ensure that their personnel are always prepared to protect lives and properties with utmost efficiency.
Emergency Preparedness through Maintenance
Implementing routine checks for fire gear readiness
Implementing routine checks for fire gear readiness is an essential step in ensuring that fire departments can respond quickly and effectively to emergencies. These checks involve a comprehensive review of all fire fighting equipment, from helmets and gloves to hoses and fire trucks, ensuring everything is in optimal condition, and ready for immediate use. Routine checks should go beyond superficial inspection to include testing equipment functionality, such as water flow through hoses, the operational efficiency of pumps, and the proper working condition of communication devices. This practice not only enhances the preparedness of the fire department but also instills confidence in the community they serve, assuring them that the first responders are equipped to handle any situation.
Performing maintenance on fire equipment before and after emergencies
Performing maintenance on fire equipment before and after emergencies is crucial in maintaining the longevity and functionality of these life-saving tools. Before an emergency, a thorough check ensures that all equipment is operational and any potential issues are addressed to prevent malfunction during critical operations. This preemptive approach can be seen in the careful inspection and servicing of apparatus and gear, highlighting the proactive steps taken to safeguard the readiness of fire response units. After an emergency, maintenance takes on a restorative role, focusing on cleaning the equipment to remove contaminants, assessing for damages incurred during use, and repairing or replacing components as necessary. This cycle of pre- and post-emergency maintenance ensures that firefighting equipment remains reliable and ready to perform flawlessly in the next call to action.
Upkeep of fire response gear to ensure peak performance during calls
The upkeep of fire response gear is a fundamental aspect of ensuring not only the effectiveness of firefighting operations but also the safety of the first responders. Peak performance during calls is achieved through a meticulous maintenance routine that accounts for the cleaning, inspection, repair, and replacement of gear and equipment. It’s not just about functionality, it’s also about protection. Maintaining the integrity of protective clothing and ensuring that communication devices are in working order is equally crucial for the safety of firefighters on the front lines.
Special attention is given to the durability aspects of the gear, considering the rough conditions under which they are used. By adopting a regimented approach to the care and maintenance of fire response gear, departments ensure that their teams are not just well-equipped but also optimally protected during their crucial work. This dedicated maintenance routine, focusing on both the operational aspects and the safety features of the gear, is what enables first responders to perform at their best, regardless of the challenges they face during emergency calls.
Fire Equipment Maintenance Practices Decoded
Firepower product inspection techniques for longevity
Inspecting fire power products requires a keen eye and a systematic approach to ensure each piece of equipment maintains its operational integrity over time. The technique begins with a visual inspection, searching for any signs of physical damage, wear, or corrosion that could compromise performance. It’s important to look beyond the surface, checking the functionality and response times of critical components such as pumps, nozzles, and electrical connectors for firefighting. To promote Fire Power’s level of longevity, these inspections should be coupled with comprehensive operational tests under conditions that mimic real-world use.
Further enhancing inspection techniques involves leveraging technology and tools designed specifically for this purpose. Utilizing thermal imaging cameras can help detect overheating issues in electrical systems before they lead to failure, while ultrasonic testing can identify cracks or flaws within equipment that are not visible to the naked eye. Documenting the results of these inspections systematically enables tracking the equipment’s condition over time, providing valuable data to inform maintenance schedules and replacement cycles. These meticulous inspection practices underscore the commitment to preserving the long service life and reliability and mimic many of the tests Fire Power products go through during production, ensuring all equipment maintains the highest standard of reliability.
Best practices for fire equipment care and service guidelines
Adhering to best practices for fire equipment care significantly contributes to the effectiveness and safety of first responders. The cornerstone of these practices is following the service guidelines provided by the manufacturers, such as Duraline. These guidelines can offer detailed procedures for cleaning, inspecting, and servicing equipment, encompassing everything from protective clothing to sophisticated firefighting apparatus. It is vital to use recommended cleaning agents and techniques to avoid damaging sensitive components, while also ensuring that the equipment is thoroughly dried to prevent mold or mildew growth.
Regular calibration of measuring instruments and updates of software in technologically advanced equipment ensure accuracy and functionality. Moreover, involving trained technicians for specialized maintenance tasks helps in maintaining high standards of care. Departments should also include a buffer in their maintenance scheduling to account for unexpected repairs or servicing needs, ensuring that equipment downtime does not affect operational readiness.
Maintaining Duraline fire power products for reliability in firefighting
The reliability of Duraline Fire Power products in firefighting hinges on proactive and comprehensive maintenance strategies. These strategies involve routine checks, prompt repairs, and adherence to a rigorous preventive maintenance program. Paying special attention to the components that connect to Duraline connectors, can prevent catastrophic failures during critical firefighting operations.
In addition to physical maintenance, keeping software and firmware within these products up-to-date ensures that the equipment maximizes its potential and compatibility with other devices. Training personnel on the proper use and immediate post-use care of equipment minimizes risks of accidental damage and extends the service life of these vital tools. Establishing a culture of responsibility and awareness among first responders about the importance of equipment maintenance ensures that Duraline Fire Power products remain a reliable ally in the unforgiving arena of firefighting.
Turning Up the Heat on Fire Gear Upkeep
Maintaining fire gear is not just a duty, it’s a commitment to operational excellence and to the first responders who rely on this equipment for their safety and that of the community. With Fire Power Products from Duraline, this commitment is underscored by our dedication to producing equipment that withstands the rigors of the job. Here, we turn up the heat on fire gear upkeep, focusing on how a culture of meticulous care can empower first responders with reliable and durable equipment.
A Commitment to Excellence in First Responders Equipment Upkeep
The upkeep of first responders’ equipment is a cornerstone of operational excellence for any fire department. This commitment goes beyond periodic checks, it’s about ingraining a regimented culture among all team members, emphasizing the critical nature of their gear’s reliability. Ensuring the longevity of Fire Power products starts with rigorous training programs focused on the proper handling, storage, and maintenance techniques specific to each piece of equipment. By addressing the unique challenges of maintaining fire-fighting gear, departments can avoid preventable malfunctions that could compromise their response capabilities. Regular updates and adherence to manufacturer guidelines ensure that all equipment meets the highest standards of operational readiness and safety.
Cultivating a Culture of Meticulous Care for Fire-Fighting Equipment
Creating a culture of meticulous care starts with leadership setting the standard and expectations for equipment maintenance. This culture is about more than just cleaning and inspecting, it involves a deep understanding of the equipment’s role in saving lives and properties. All personnel must be trained in advanced cleaning techniques, which not only preserve the integrity and functionality of the gear but also ensure the health and safety of the first responders by preventing exposure to harmful contaminants. Incorporating regular feedback sessions where team members can share best practices and challenges fosters a collaborative environment dedicated to continuous improvement in gear upkeep.
Empowering First Responders with Reliable and Durable Fire Power Products
Empowering first responders begins with the assurance that their equipment will perform to the highest standards when it matters most. This assurance comes from the combination of high-quality parts and a relentless maintenance regimen. Durability and reliability are the hallmarks of Duraline’s Fire Power products, designed to endure the harsh conditions encountered during firefighting and emergency responses. By emphasizing proactive care, including the routine check for wear and using products designed for fire fighting’s harsh environment, departments can significantly enhance the operational life and bring all equipment up to the standards set by Fire Power.
A robust program for the upkeep of firefighting equipment includes not only cleaning and inspection routines but also investing in training and development. This ensures the personnel are well-versed in the latest maintenance techniques and technologies. Consequently, first responders feel confident in their gear’s reliability, allowing them to focus on the critical tasks at hand, secure in the knowledge that their equipment will not let them down.
With a dedication to quality, innovation, and support, Duraline is committed to ensuring that fire departments are equipped with the best tools in the industry. Through meticulous upkeep, these tools remain dependable and ready to rise to the challenges of fire fighting and emergency response, fulfilling our commitment to those who safeguard our communities.